The Camosun Innovates (CI) team at Camosun College is helping in the fight against COVID-19 by creating acrylic 20-row trays to carry vials of the Pfizer-BioNTech COVID-19 vaccines. CI applied research technologist Matt Zeleny says each vial carries between five and six doses of the vaccine. The vaccine has to be kept at -70 C and has to be loaded into the tray in under three minutes, he says, which rules out doing that by hand. Zeleny created what they’re calling the “Camosun VI-grip” to lower handling time using a “simple two-piece kitchen scissor design.”
“The province can now precisely target and distribute these vaccines in whichever quantities are required,” he says.
Before CI came up with its idea for a tray, the vaccines were shipped in “a small pizza box jam-packed with 195 vials,” says Zeleny. The trays created by CI cut down on waste and ensure as many vaccines as possible get used, he says, adding that the vaccine is one of the most critical tools the government has right now. Before CI came up with the trays, they were approached to print blank vials to fill the empty spots in those original trays.
“When you remove any of the vials from that [original] box, it creates a void that they can slosh around in, and if that happens in its frozen state, it can actually denature the vaccine, rendering it useless. It’s a big risk,” he says. “[The British Columbia Centre for Disease Control] [BCCDC]… came to us to ask if we could 3D print fake vials that they could use to occupy those spaces.”
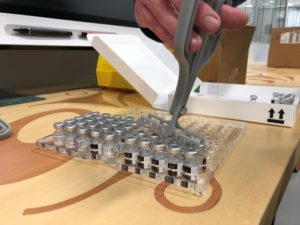
Zeleny says that none of the 3D printing materials CI has can sustain the low temperature, so he looked into what materials would work; acrylic was one of them.
“[We] got started on manufacturing 1,000 blanks for them,” he says. “In that process, we also pitched maybe creating an acrylic tray that would be able to hold the vials stably.”
Zeleny redesigned the tray so that they were rows of five interconnected holes that would be easy to count at a glance, he says.
“The VI-grip basically grabs five vials at a time and populates a full row,” he says.
Zeleny says the design time aspect of the project took him about seven hours. The rest was all production time.
“It takes about two and a half hours to produce 25 of those trays,” he says.
Zeleny says that while it feels really good to be able to turn a product around that quickly, it’s just business as usual.
“It’s honestly not that different from what I do everyday, anyway,” he says.
The tray design took him about 45 minutes to draw, and iteration took another 20; the longest part of the process was the VI-grip, he says.
“It was really just sort of seeing it in your mind and then actually delivering it as a tangible item, a drawing that you can manufacture from,” he says.
CI is also on standby, he says, for when the province receives other brands of vaccines, and are just waiting to hear back from the BCCDC about their thoughts on CI’s design.
“We have also delivered six prototypes of a foam holder for pre-drawn Moderna doses, he says. “We’re just waiting for some feedback on that.”